Bamboo decking is a popular choice among homeowners and builders looking for a sustainable and durable option for their outdoor spaces. As we’re bamboo deck manufacturer and we know that the bamboo decking production process is a complex and delicate process that involves several stages to ensure the final product is of the highest quality.
From the selection of raw materials to the final finishing, each step plays a crucial role in determining the strength, stability and longevity of the finished product. In this article, we will explore the different stages of the production process and how they contribute to the final outcome of a high-quality bamboo deck.
1, Cutting down bamboo logs to the same size
The process of producing bamboo decking begins with the selection of high-quality bamboo logs that have reached a maturity of 5-6 years. These bamboo logs are then carefully cut down to ensure that each log is of the same size and diameter, typically larger than 10cm.
The cutting process is crucial in determining the quality of the final product and is carried out with precision to minimize any waste. The large bamboo culms are then cut into smaller strips, which are ready to undergo further processing and treatment to become bamboo decking boards.
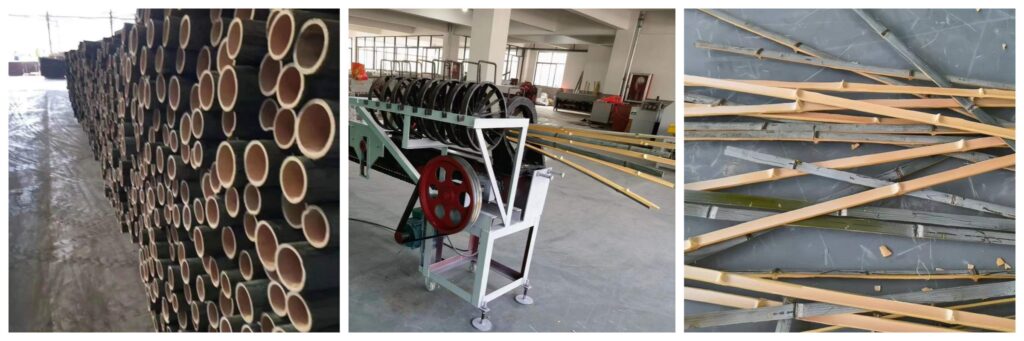
2, Stem to strip
The next step is the removal of the outer skin (organic green layer) and inner skin (yellow layer) of the small strips. This process is called “Striping off” and is crucial in revealing the inner fibers of the bamboo, which will be used in the final product. Once the strips have been stripped of their outer and inner layers, they are then pressed into strands, which will later be pressed together to form the decking boards.
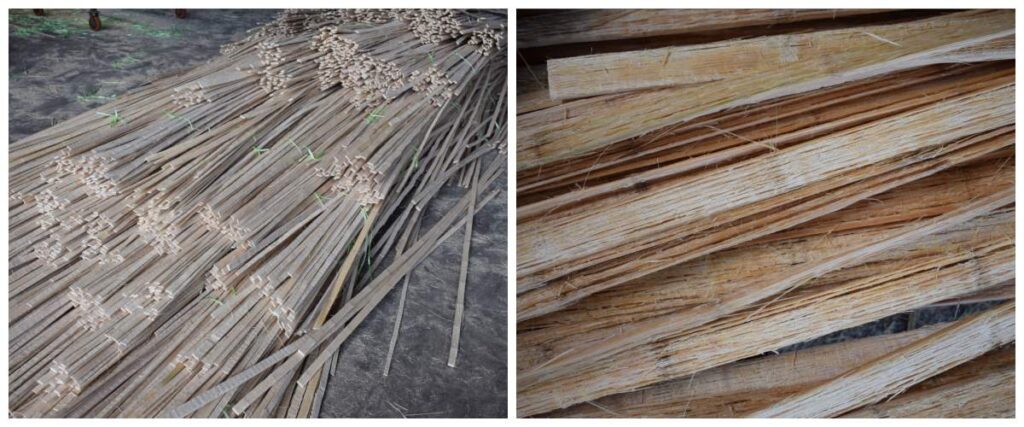
3, Carbonized
The carbonization process is a key step as it helps to enhance the durability and stability of the bamboo fibers. The bamboo strands are subjected to high heat and steam, either at 140°C or 220°C, to remove the starch and sugar content in the bamboo.
This process of carbonization gives the bamboo fibers a distinctive color and character, depending on the temperature at which it is performed. Bamboo strands that are carbonized at 140°C have a light brown color, while those carbonized at 220°C take on a dark chocolate hue. This color difference is due to the extent of caramelization of the sugars in the bamboo fibers.
In addition to the carbonization process, the bamboo strands also undergo a deep anti-mold treatment. This treatment helps to protect the bamboo decking from the growth of mold and mildew, ensuring that it retains its appearance and performance even in humid environments. The deep anti-mold treatment is achieved through a specialized process that provides an extra protection for the bamboo fibers.
The end result is a high-quality bamboo decking product that is durable, stable, and resistant to mold and mildew, making it an ideal choice for outdoor use. The combination of carbonization and deep anti-mold treatment ensures that the bamboo decking is ready to withstand the rigors of daily use and the elements, making it a long-lasting and low-maintenance decking solution.
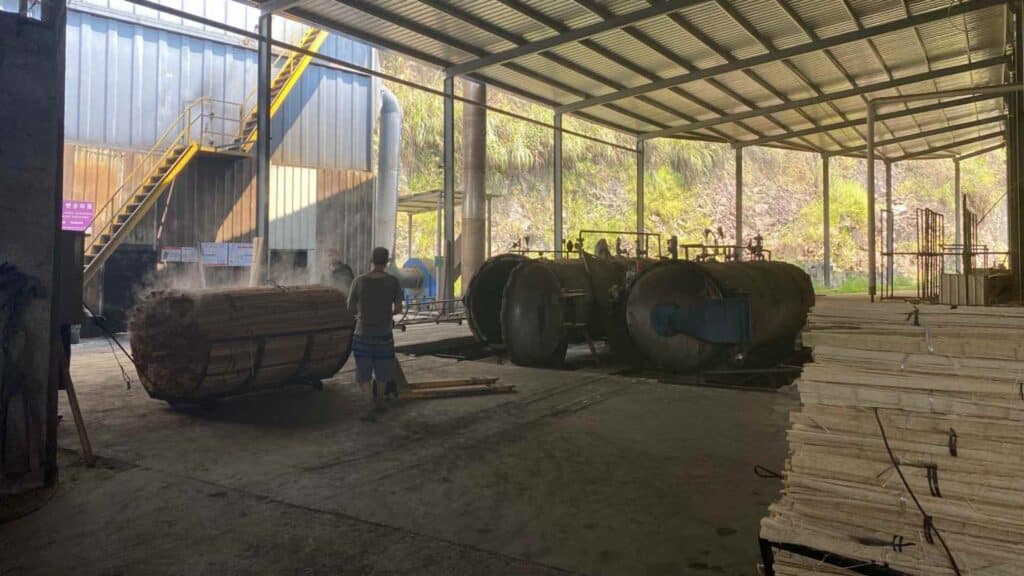
4, Drying
This is a crucial step as it helps to lower the moisture content of the carbonized bamboo strands to below 5%. When the moisture content is at this level, the bamboo fibers are able to absorb the environment-friendly phenolic resin in the most efficient manner, strengthening and stabilizing the fibers.
The drying process is carried out in a controlled environment to ensure that the moisture content is reduced to the desired level and that the bamboo fibers are ready for the final stages of production. The drying process is essential in ensuring that the final product is of high quality, with a stable structure and a consistent appearance.
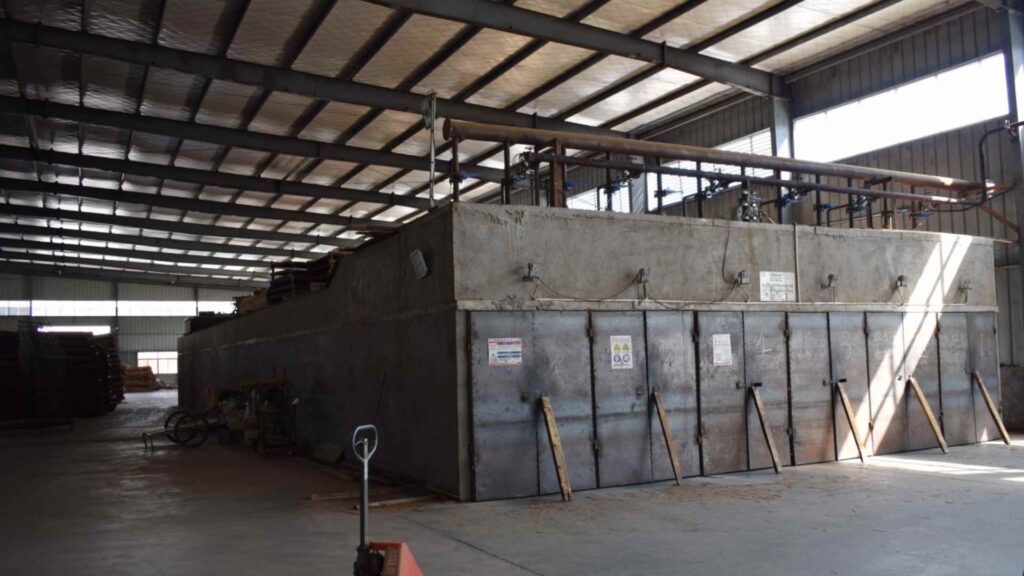
5, Impregnation
This process involves soaking the dried and carbonized bamboo strands in phenolic resin. The use of ANOS® technology during the impregnation process ensures that the final product is of premium quality, with a high level of resistance to moisture, weathering, and other environmental factors.
After the bamboo strands are thoroughly impregnated with phenolic resin, they are then placed in a drying kiln. They remain there for 15 days, in a room that has a balanced temperature and humidity level, to allow the desired moisture content to be achieved. This controlled environment helps to ensure that the moisture is evenly distributed, resulting in a bamboo decking product that is of high quality and consistent appearance.
6, Hot Pressing
Hot pressing process involves applying high temperature and pressure to the impregnated bamboo strands, using a 3,000-ton large press, to fuse the bamboo and phenolic resin into high-density bamboo boards. The resulting boards have a density greater than 1200 kg/m3, making them much harder and more durable than traditional hardwood decking materials.
The high-pressure pressing process results in a dense and stable product, but it can also create molecular stress within the material. To ensure that the final product is of the highest quality, the bamboo panels are then left to rest for 7-10 days to release any molecular stress that may have been created during the hot pressing process. This also allows for improved stability and durability, ensuring that the final product is of consistent quality and has a long service life.
If the bamboo deck panels are not allowed to rest for a sufficient amount of time, the inability to release built-up stress can result in warping and deformation of the finished product. The duration of the resting period is critical to ensuring the stability and longevity of the bamboo deck panels.
7, Cutting & Forming
After the hot pressing process, the full-size bamboo panels are cut into smaller, regular sizes to meet design specifications. Additionally, the panels can also be processed into different widths to meet the specific requirements of a project.
The cut bamboo panels are then formed into different profiles, such as big wave, small wave, flat, and small groove surfaces, to give the decking a unique and attractive appearance. This process of cutting and forming ensures that the bamboo decking fits seamlessly into any outdoor design and provides a custom and tailored solution for a wide range of applications.
8, Finishing
The final step in the production of bamboo decking is finishing, which gives the decking its final look and protection against the elements. The finishing process involves a comprehensive, ultra-long painting production line that combines multiple steps to ensure a high-quality finish.
The process begins with dust removal, where any remaining dust or debris is removed from the surface of the bamboo decking. The decking is then coated with oil, which provides a protective barrier and enhances its natural beauty. The oiled decking is then dried in a board drying process to ensure that the oil is evenly distributed and properly absorbed.
Once the drying process is complete, the decking is re-oiled and re-dried to provide an additional layer of protection. This step ensures that all sides of the boards are thoroughly sealed with Woca oil, which provides excellent resistance against moisture, UV radiation, and other environmental factors.
In conclusion, the finishing process is a crucial step as it provides the final look and protection that is essential for long-lasting performance in outdoor environments. The end result is a high-quality, attractive, and durable product that provides a sustainable and low-maintenance alternative to traditional decking materials.
References
How To Judge The Quality Of Bamboo Deck
How to Correctly Choose Bamboo Products in Different Climates?
3 Responses
Hi Allen , Thanks for the above Article , i am from india and we are planning to setup a factory for the bamboo decks and other bamboo items. Can we get connected for further information
Thanks
Santosh Kulkarni
‘
Hi Santosh,
Of course, you can send messages to my email box.
You could certainly see your expertise in the paintings you write. The world hopes for more passionate writers such as you who are not afraid to say how they believe. Always go after your heart.